Application Notes:
Efficient laser cleaning prior to laser welding of transmission components without an optical scanner
Task:
- Improve welding quality
- Replace chemical and abrasive cleaning
Nowadays, laser welding is a widely used practice in automotive and aerospace industries. However, it is not defect free, especially in welding of aluminum alloys. Laser welding often produces low tensile strength joints due to porosity caused by contamination of the welding region prior to welding. Similarly, surface organic contaminants, such as grease, oil, corrosion inhibiting agents, and other typical compounds used in manufacturing, are often present on steel parts prior to welding which results in cracks and porosity in the welds. Thus, it is required to clean the welding region prior to welding to ensure geometrically correct and defect-free joints. Usually, abrasive or, more often, chemical techniques are implemented. There are, however, obvious disadvantages associated with these conventional methods:
· poor or no control – low accuracy and repeatability
· possible damage to the part
· hazardous waste
· disposal of cleaning material
· significant manual labor
· significant machine down-time
· cannot be performed in-line with the welding process
Laser pre-welding cleaning is a “green” approach to this problem. It is efficient, fast and offers advantages over the above-mentioned methods:
· parts stay on-line
· fast processing
· more efficient contamination removal
· no waste
· low maintenance
· fully automated
Laser pre-welding cleaning, however, requires an optical scanner to operate. Using an optical scanner has its disadvantages that make laser cleaning less appealing: low duty cycle, high cost, regular maintenance, programming and operator input, cooling when used with high power lasers. That, normally, drives associated costs up and makes laser cleaning unaffordable to the majority of businesses.
To remedy this flaw, we use beam delivery systems without an optical scanner to perform laser cleaning. A fiber laser processing head optics reshapes the laser beam to produce a thin line on a work-piece to maximize the energy density of the beam.-
To demonstrate the efficiency of the aforementioned optical delivery system, we laser cleaned and laser welded transmission components that were known to have welding defects when not pre-cleaned as described below. Fig. 1 shows parts to be jointed. It is obvious that the V-grove joint region is contaminated with oil. If not pre-cleaned, the laser welding results in a very poor quality joint with a number of defects as shown in Fig. 2. However, when a similar part has the V-grove laser pre-cleaned prior to welding, no weld defects are observed.
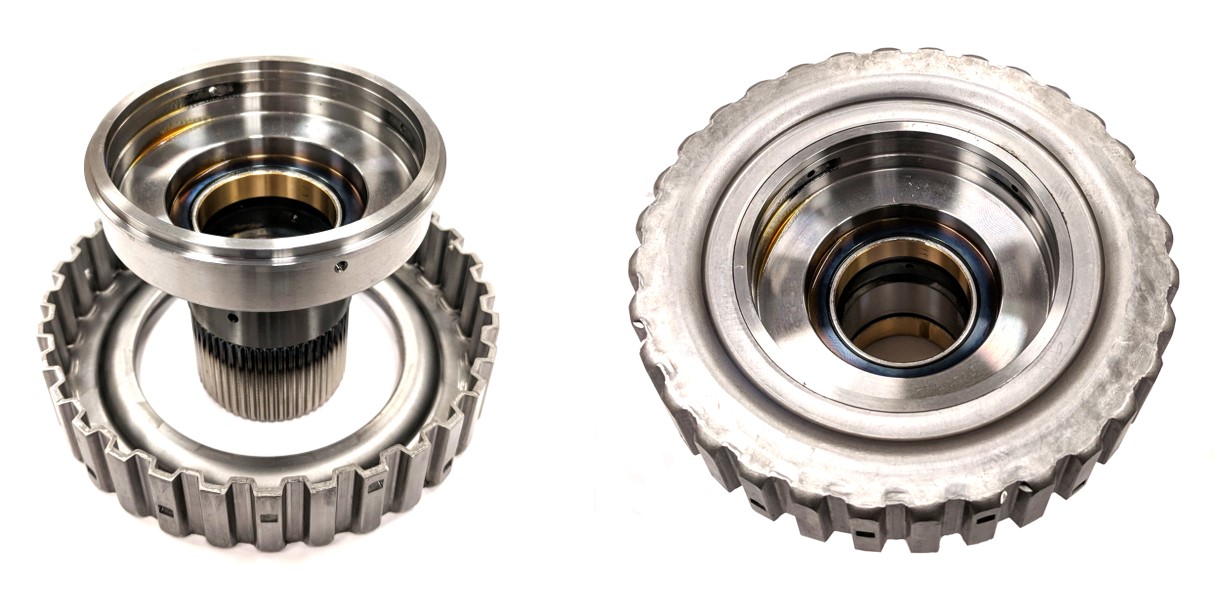
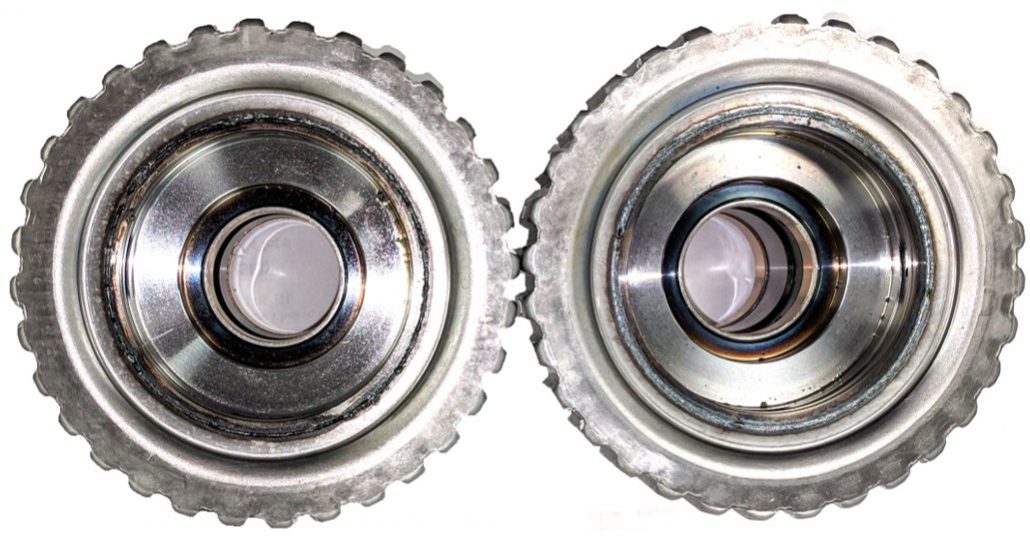
To prove an importance of laser pre-welding cleaning, we contaminated each part’s welding region with a different common organic compound, such as oils with rust and corrosion inhibiting agents, cutting fluids and lubricants, zinc sprays and gels for anti-corrosion coating (such as TEROSON VR 4600), and liquid paint markers (used in corrosion resistance applications). Parts are then mounted on a FANUC robot, as shown in Fig. 3, that is programmed to perform one full rotation. The fiber laser processing head with the line-shaping optics is fixed opposite to the part, and the laser is turned on to clean only half of the V-grove’s length. The part is then laser welded and cut in several places to examine and compare welding quality in the laser treated and contaminated regions of the same part.
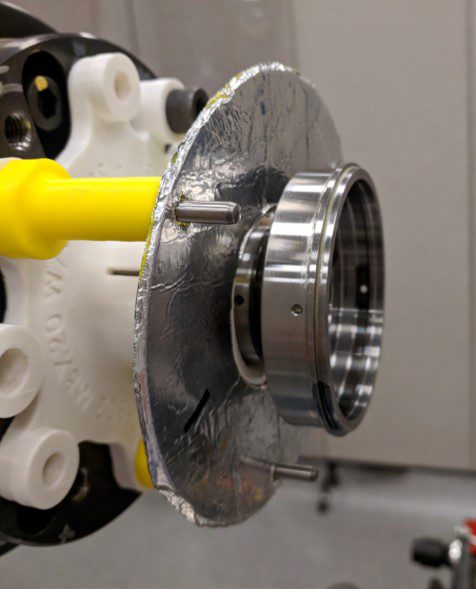
To create a narrow line that fills the whole V-grove to be cleaned in one pass, ALE 010034 welding head was used. This fiber laser processing head is inexpensive and yet very versatile that allowed us to simply replace focusing components with a beam shaping module. A video below shows a laser cleaning process. It is fast and very efficient. All the contaminants we tried were removed completely in just 3 seconds.
After the pre-welding cleaning, parts were marked, laser welded, and cut to examine the weld quality as shown in Fig. 4 and 5.
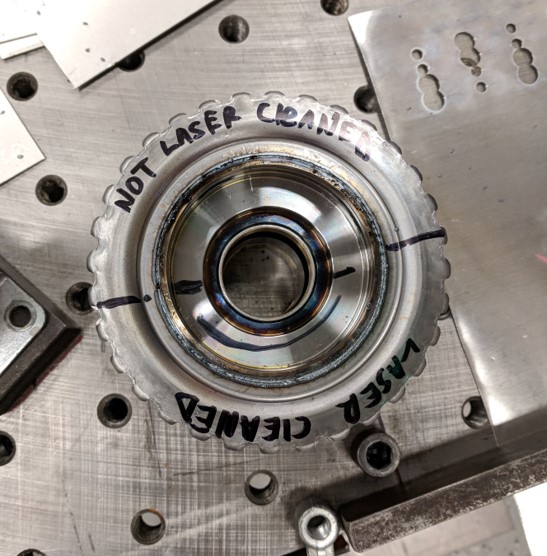
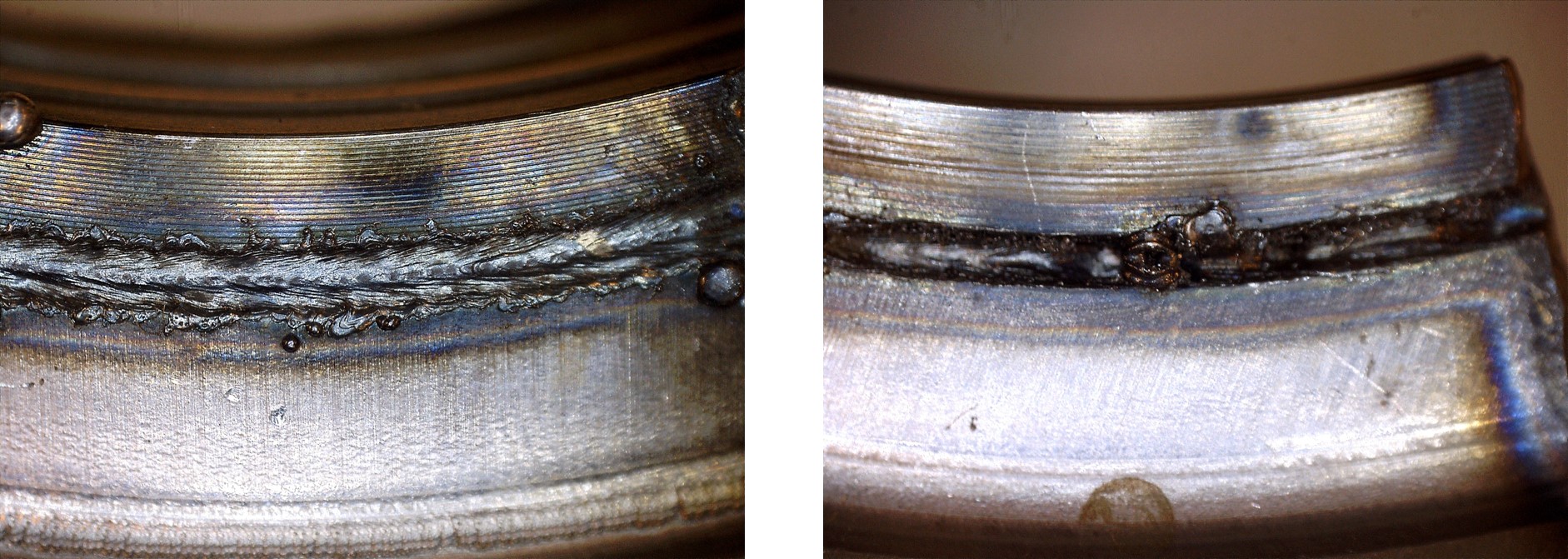
Below are typical examples of the weld cross sections for some of the contaminants used in this study.
no laser cleaning
contaminant: oil with corrosion inhibiting agents
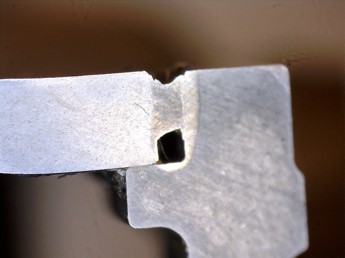
contaminant: cutting fluid
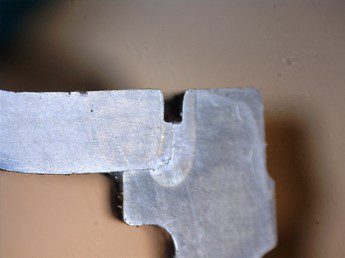
contaminant: zinc adhesive gel
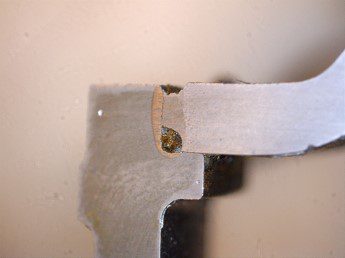
laser cleaned
contaminant: oil with corrosion inhibiting agents
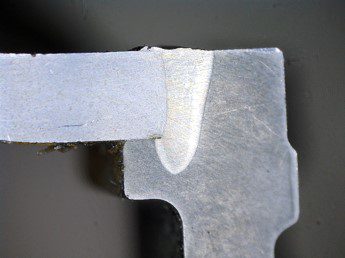
contaminant: cutting fluid
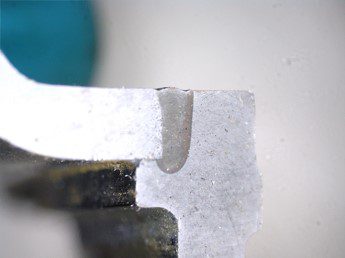
contaminant: zinc adhesive gel
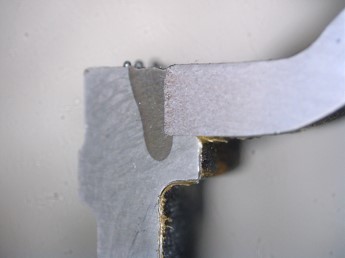
Our study showed that:
1. Contamination of the welding surface causes strong welding defects, including cracks and porosity.
2. Laser pre-welding cleaning technique we used:
· Completely removes contamination
· Significantly improves welding quality
· Can be accomplished on-line, is fully automated and fast (under 3s/part)
· Improves corrosion resistance and adhesive properties of steel
· Does not require expensive optical scanning devices
Moreover, this method can be used for a variety of application where it is required to cover a large area, but an optical scanning device makes utilizing a laser unaffordable, such as:
· Laser cleaning of Al alloys to remove oxide layers
· Plastic thermal welding
· Plastic or rubber mold cleaning
· Wire stripping
Overall, laser preweld cleaning is an efficient and cost-effective technique that can be beneficial for small and giant businesses alike. American Laser Enterprises provides expertise in building custom units that can be integrated into your process, starting from initial consulting to a complete integration. Please contact us to discuss your needs!
We would like to thank Jon Delboy, Roger Schmidt, and Peter Busuttil at KUKA Systems Development Center for their help fulfilling this project.